This post contains images with emotional impact.
A new video about WTC popped on youtube which prompted me to write this blog post because i suspect the number of casualties by dust, unreported to this day, where many times more than those who died in the towers.
04/09/2019 Video is gone, can't find quickly a similar one without the offensive music. Here are some pictures showing the scale of the disaster brought by dust. I don't believe people could really survive in that dust for more than a few seconds.
Until WTC designed by architect Minoru Yamasaki and after, all high rise steel constructions were done in the "classic" fashion with structural vertical and horizontal rolled steel beams with cross reinforcement joints and numerous interior walls. As the looks suggests, this type of design is solid and can't be easily damaged.
WTC structure was made only of two so called tubular frames or cages, using about half the steel the old design uses. Outer frame was made of prefab panels that were actually made of three vertical, square section, rolled steel beams (2nd image below) welded together with other three huge pieces of sheet metal. This image, like many others, is tricky cause it suggests the building in the distance was built in a similar way. It only appears so because of its shape, no other building has ever been designed in this way.
The prefab panels themselves seem to be inspired from a Buddhist architecture ornament called Torana. (Torre means tower in Spanish and Italian, and toro means bull with two horns of course).
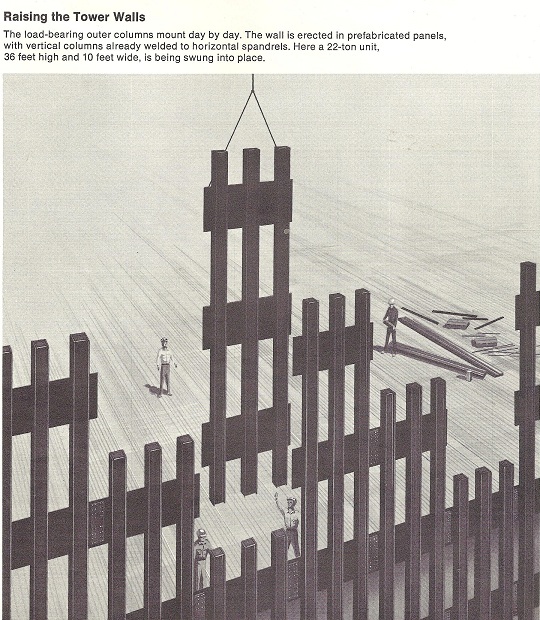
Panels were put together in a new, revolutionary, also unique design: An outer tubular frame made of prefab inter-positioned panels (outer cage) and an inner core of "classical design" (inner cage), though only for elevator and shafts, with vast floors in between that were connecting and preventing the inner and outer cage to sway or buckle (bend) in or out.
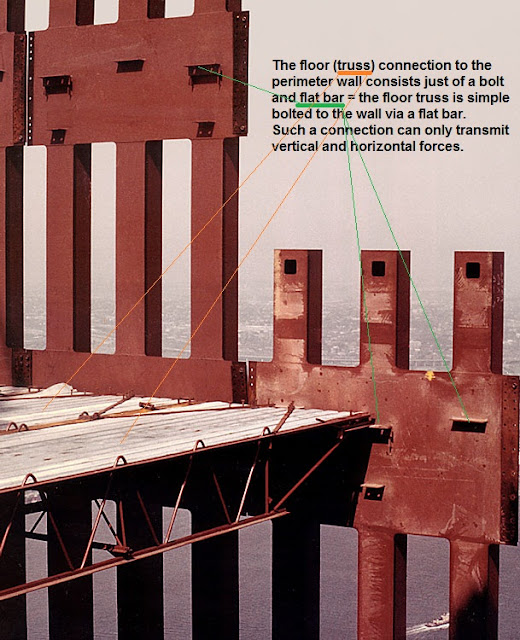
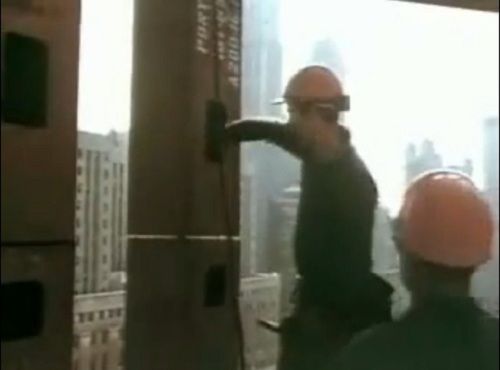
Outer frame panels are connected together with four bolts at the end of each rolled steel square tube.
This type of joint would take a lot of vertical compression, as much as allowed by the rolled steel maximum compression load, some horizontal or side compression, limited by the bolts, (which have a cross section far less than of the cross section of the rolled steel) and could take almost no bucling (bending in and out of the cage wall) because of the prying effect on the bolts at the joint level.
Buckling and shear of the outer cage was was dealt with by inter-positioning of the of the panels and by floor trusses between inner and outer frame (cage) which allowed the construction to stay vertically.
I tried to search to see how many bolts held together the structure and could not find. It's 12 per each prefab panel. Can't find how many panels either. What i found is many other analysis were blaming the bolts for the failure. But not those, the bolts holding together the floor trusses to the walls.
Even with this design (outer-inner cage) building would have behaved differently if the vertical square rolled beams making the outer cage where of one piece from bottom to top or anyways, fewer than one per 3 floors or assembled with a smaller square beam in between called "inner sleeve". This type of joint can take almost as much bending (side compression), shear and buckling as a continuous beam.
When assembled, however, the building had the appearance of outer cage beams being continuous also because of the aesthetic aluminum cladding installed on the outside on top of the each beam. From one of the images below it results some 258 vertical (interrupted every 3 floors) beams all around the building, which makes for 86 panels per each 3 floors, 110 floors, resulting approximately 4,730 prefab panels and 56,760 structural bolts (and nuts). Most of these bolts popped during cascading failure of the building, which apparently was designed in such a way that each the concrete floor turned into dust when falling onto next.

These are called bridge trusses making up the vast floor and connecting inner and outer cages. Thin, nothing like the sound, solid "classical" design seen in the second picture in this post (above), used in all high rise buildings before and after.
This design provided indeed ample floors with no walls in between.
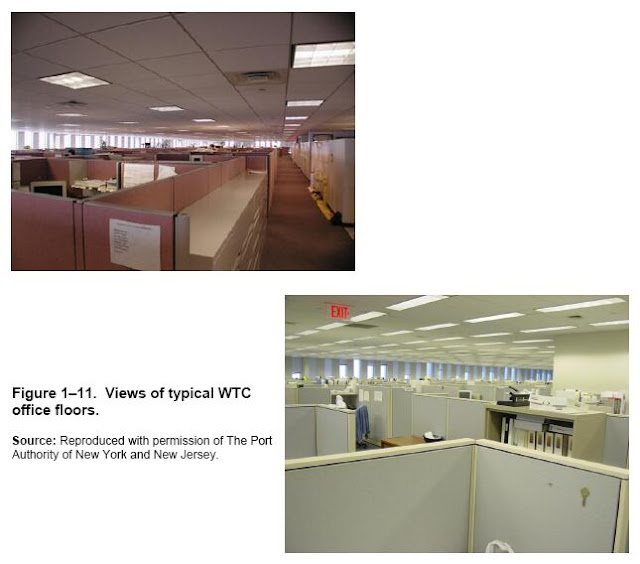
21 Floor covering
22 In-situ concrete (4 inches)
23 Trough decking (1 1/2 ", ribbed)
24 Bar joist
25 Electrical services duct
26 Air-conditioning duct

In this image after first impact on South Tower or WTC2 one can see prefab panels taken as a whole at least at one end, caused by failure of bolts. Pieces of the concrete floor missing.
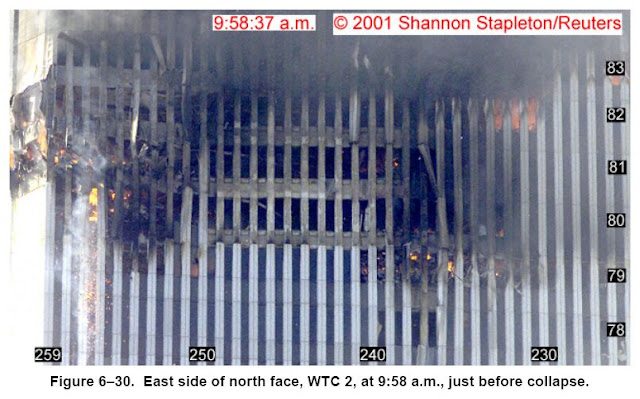
This is a picture of the the exit area of the first hit tower. It was not until i have seen this picture that i realized the failure started at the concrete and steel components of the floors.
After impact, fuel spread across the vast floors caught fire and the expanding concrete and metal trusses making the floor heated by fire started to push, mainly alongside the trusses, and steel decking ribs on top, inner and outer cage against each other in the same time with floor buckling of the floors in other places creating a prying effect on the bolts connecting connecting trusses with the cages and those connecting panels with each other. Floor's structural role in stabilizing the sway of the outer cage in this case reverted to causing buckling of the cage caused by floor elongation (by heat expansion) and gradually breaking the bolts between panels and between cages and floors by prying effect. When enough of those bolts broke the floors started to fall onto each other.
Towers' "revolutionary" tubular design made of only two cages (tubes) (inner and outer) had several major design flaws.
Vast, relatively thin floors, where floors were/are also made of rolled steel beams played only a "minor structural role" compared to outer and inner frame, except sustaining selves, the concrete, and holding the outer cage to prevent sway or buckling. Without floor trusses and steel decking connecting inner and outer cage, the outer cage could not keep its shape, but sway, buckle, or bend inward or outwards and break.
When assembled, however, the building had the appearance of outer cage beams being continuous also because of the aesthetic aluminum cladding installed on the outside on top of the each beam. From one of the images below it results some 258 vertical (interrupted every 3 floors) beams all around the building, which makes for 86 panels per each 3 floors, 110 floors, resulting approximately 4,730 prefab panels and 56,760 structural bolts (and nuts). Most of these bolts popped during cascading failure of the building, which apparently was designed in such a way that each the concrete floor turned into dust when falling onto next.
These are called bridge trusses making up the vast floor and connecting inner and outer cages. Thin, nothing like the sound, solid "classical" design seen in the second picture in this post (above), used in all high rise buildings before and after.
This design provided indeed ample floors with no walls in between.
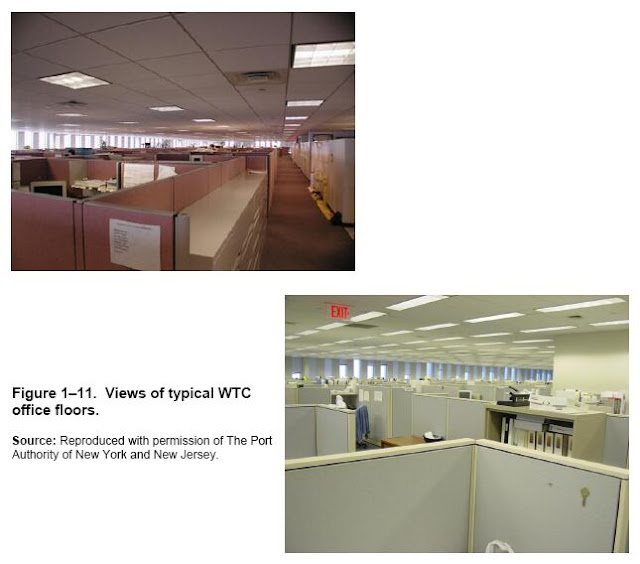
21 Floor covering
22 In-situ concrete (4 inches)
23 Trough decking (1 1/2 ", ribbed)
24 Bar joist
25 Electrical services duct
26 Air-conditioning duct

In this image after first impact on South Tower or WTC2 one can see prefab panels taken as a whole at least at one end, caused by failure of bolts. Pieces of the concrete floor missing.
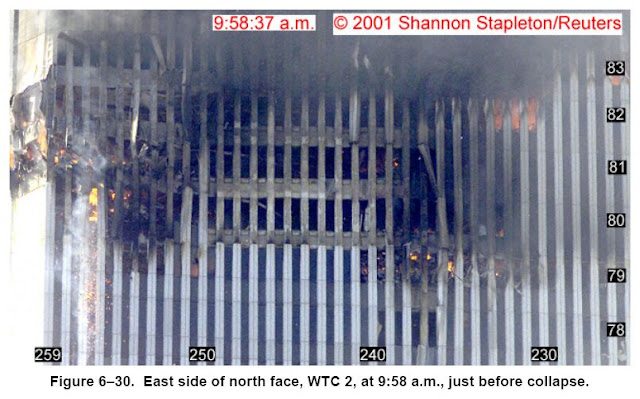
This is a picture of the the exit area of the first hit tower. It was not until i have seen this picture that i realized the failure started at the concrete and steel components of the floors.
After impact, fuel spread across the vast floors caught fire and the expanding concrete and metal trusses making the floor heated by fire started to push, mainly alongside the trusses, and steel decking ribs on top, inner and outer cage against each other in the same time with floor buckling of the floors in other places creating a prying effect on the bolts connecting connecting trusses with the cages and those connecting panels with each other. Floor's structural role in stabilizing the sway of the outer cage in this case reverted to causing buckling of the cage caused by floor elongation (by heat expansion) and gradually breaking the bolts between panels and between cages and floors by prying effect. When enough of those bolts broke the floors started to fall onto each other.
Towers' "revolutionary" tubular design made of only two cages (tubes) (inner and outer) had several major design flaws.
Vast, relatively thin floors, where floors were/are also made of rolled steel beams played only a "minor structural role" compared to outer and inner frame, except sustaining selves, the concrete, and holding the outer cage to prevent sway or buckling. Without floor trusses and steel decking connecting inner and outer cage, the outer cage could not keep its shape, but sway, buckle, or bend inward or outwards and break.
About half of the weight of the floors was supported by a single shell or the outer cage with lack of redundancy. When that frame failed, there was nothing else to prevent the whole building from collapsing.
Ultimately, lack of inner walls and vastness of the floors due to unique design contributed to spreading of fuel and fire almost instantly to an entire half of the building (on several floors), when the floor expanded, heated by fire, and because of the length, the expansion was in the range of several feet.
Thermal expansion during hot summer days and the contraction in the winter times is the reason all bridges made of steel reinforced concrete have expansion gaps, while the roads themselves loose enough heat to the ground underneath not to expand and buckle. But if the temperature raised not with 20 or 50 degrees or whatever but with several hundred degrees, those gaps would not be enough. There is also a thermal inertia which prevents the bridge from heating all the way during the summer days while cooling during night time
Unusual hot summer may have been the cause for collapsing of that bridge in Genoa, Italy.
Another examples of metal structure that expand with heat was supersonic Concorde' fuselage. At 2 times the speed of sound, because of intense friction with the air, Concorde's (and other's supersonic planes) fuselage was expanding as much as one foot while of course the cabin's floor inside stayed at room temperature).
"heating had a significant impact on the construction of Concorde. Perhaps the most important issue designers had to contend with was the fact that heat causes materials to expand. I've seen different values on exactly how much the aircraft expanded, but most sources indicate that the air-frame stretched by 5 to 12 inches (12 to 30 centimeters) at Mach 2. Given the aircraft's normal length of 204 ft (62.2 m), that change amounts to little less than a 5% increase in the size of the Concorde fuselage."
http://www.aerospaceweb.org/question/planes/q0199a.shtml
Another examples of metal structure that expand with heat was supersonic Concorde' fuselage. At 2 times the speed of sound, because of intense friction with the air, Concorde's (and other's supersonic planes) fuselage was expanding as much as one foot while of course the cabin's floor inside stayed at room temperature).
"heating had a significant impact on the construction of Concorde. Perhaps the most important issue designers had to contend with was the fact that heat causes materials to expand. I've seen different values on exactly how much the aircraft expanded, but most sources indicate that the air-frame stretched by 5 to 12 inches (12 to 30 centimeters) at Mach 2. Given the aircraft's normal length of 204 ft (62.2 m), that change amounts to little less than a 5% increase in the size of the Concorde fuselage."
http://www.aerospaceweb.org/question/planes/q0199a.shtml
Thermal expansion by heat was the direct cause of failure of only one or two floors. But when those floors fell on to the next one the accumulated weight of all the above floors accelerated by gravity lead to a cascade failure of all the other floors and corresponding walls of the cages. Concrete component of each floor, that was made by a certain recipe, was turning explosively into dust upon hitting the next floor.
There is little doubt in my mind that the towers were designed on purpose like a card castle, to create some day, when the right moments arrives, this type of spectacular frightening failure.
There is little doubt in my mind that the towers were designed on purpose like a card castle, to create some day, when the right moments arrives, this type of spectacular frightening failure.
When re-editing this post and was searching for different shapes (sections) of rolled steel (for the purpose of further documenting this blog post) and on a site i found out some shapes are no longer available as a result of America's steel industry decline. There are probably also not many civil engineers left to deal with these kind of things or write on blogs or on forums and actually no more high rise buildings to be built. Or too few to matter.
No comments:
Post a Comment
Friendly comments welcome
Note: Only a member of this blog may post a comment.